Sustainable Compressed Air,
Without the Waste
Reduce your carbon footprint & improve efficiency
with DIRECTAIR®
The DIRECTAIR® Difference
Compressed air is essential in manufacturing, but traditional systems waste up to 80% of their energy as heat. That loss leads to higher emissions, excessive energy bills, and unnecessary maintenance. DIRECTAIR® eliminates that waste. By delivering compressed air as a utility, it removes the cost and complexity of owning and maintaining outdated systems, while improving performance across the board.
DIRECTAIR® is built for efficiency. Through proactive management and real-time monitoring, it reduces emissions, costs energy use, and extends equipment life. DIRECTAIR® turns compressed air from a hidden liability into a high-performing utility that support environmental goals, lowers operational costs, and drivers sustainability results.
This is a placeholder for the video description.
Please click here to view the video transcripts
The Sustainable Impact of DIRECTAIR®
Since its inception, DIRECTAIR® has helped businesses operate more efficiently while significantly reducing their environmental footprint. With over 18.5 million hours of operation, DIRECTAIR® has delivered over 500,000 CFM of compressed air while optimizing system efficiency compared to traditional compressed air setups.
-
Reduced Energy Consumption
By right-sizing compressed air supply, DIRECTAIR® provides efficient systems that consume less energy, already saving customers over 550,000,000 kWh of electricity. -
Lower Carbon Emissions
DIRECTAIR® has helped customers reduce their carbon footprint by eliminating waste and operating at peak efficiency, resulting in a reduction of nearly $4 million metric tons of CO₂ emissions.
-
Predictive Maintenance & Monitoring
Advanced real-time monitoring has prevented unnecessary energy spikes and equipment failures, saving our customers nearly $418,000,000 in total energy cost savings. -
Eco-Friendly Operations
DIRECTAIR® is designed to support sustainability initiatives, including corporate ESG goals, while significantly reducing the environmental impact of industrial compressed air use.
Sustainability by the Numbers
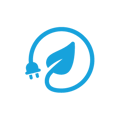
$418 Million
in energy cost savings
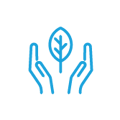
400 Million
trees
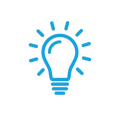
80 Million
-3.png?width=146&height=100&name=DIRECTAIR%20Iconography_clean-air%20(1)-3.png)
4 Billion Carbon Offset
DIRECTAIR® vs. Traditional Compressed Air Systems
DIRECTAIR®
- Energy Efficiency: DIRECTAIR® is up to 50% more efficient than conventional compressor rooms, delivering the air you need with zero wasted energy.
- Carbon Footprint: 3,699,801 metric tons of CO₂ saved with DIRECTAIR®, equivalent to removing 803,000 gas-powered cars from the road.
- Maintenance & Waste Reduction: DIRECTAIR® uses Predictive maintenance & 24/7 monitoring to prevent failures before they occur, reducing downtime and waste.
- Reliability & Uptime: DIRECTAIR® provides 99.9% uptime with remote monitoring and proactive maintenance.
- Lifecycle Costs: Zero capital investment - pay only for the air you use, reducing financial strain and resource waste.
- Equipment Longevity: No over-sized or overworked equipment, meaning DIRECTAIR® compressors operate at peak efficiency and last longer.
- Energy Savings: DIRECTAIR® has saved 5,218,337,179 kWh since inception—equivalent to powering 490,000 homes for a year—reducing strain on power grids and saving customers over $418 million in energy costs.
- Operational Footprint: Modular, compact units from DIRECTAIR® require no dedicated compressor room, reducing space requirements.
- Regulatory Compliance: DIRECTAIR® helps meet corporate ESG goals and aligns with ISO 50001 (Energy Management).
Traditional Systems
- Energy Efficiency: Wastes up to 50% of energy, according to the U.S. Department of Energy, due to leaks, artificial demand, and inefficient systems management.
- Carbon Footprint: High emissions due to inefficient compressors, overuse, energy waste, and lack of system optimization, leading to unnecessary environmental impact.
- Maintenance & Waste Reduction: Over 70% of manufacturers lack real-time monitoring for their compressed air, leading to energy waste and inefficiencies.
- Reliability & Uptime: Typical compressor rooms have a failure rate of 25% per year, causing unexpected downtime. Frequent breakdowns and unplanned downtime reduce operational efficiency.
- Lifecycle Costs: High capital costs for compressor room construction, plus ongoing maintenance and energy waste.
- Equipment Longevity: Overworked compressors wear out faster, requiring costly replacements and increased energy consumption to compensate for declining efficiency.
- Energy Savings: Consumes significantly more energy due to continuous operation, pressure fluctuations, and inefficiencies, leading to higher utility bills, increased operational costs, and greater environmental impact.
- Operational Footprint: Requires a large compressor room, increasing construction, facility costs, and energy consumption for climate control and ventilation.
- Regulatory Compliance: Harder to track sustainability metrics and maintain compliance with energy efficiency standards.